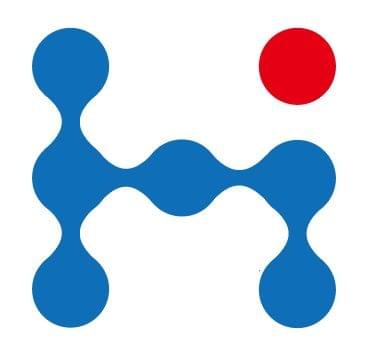
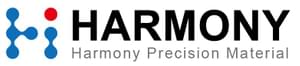
球形氧化鋁應用
一、為何選用球形氧化鋁?
球形氧化鋁是一種經過特殊造粒與高溫燒結製成的高純度氧化鋁粉體,其形狀接近完美球狀,帶來以下優勢:
1. 高導熱性:
球形氧化鋁本身具有較高的熱導率(通常可達20–30 W/m·K),能有效提升複合材料(如導熱膠、導熱填料)的整體導熱性能。2.低黏度配方:
球形結構減少了粉體之間的摩擦與堆積,使其在製作導熱膠、導熱矽膠或灌封膠時能在高填充比下維持較低黏度,提升施工與加工性。
3.優異的流動性與填充性:
球形粒子排列緊密且均勻,有助於形成連續的導熱通道。4.電絕緣性佳:
適用於需要兼顧導熱與電絕緣的電子產品。二、球形氧化鋁作為導熱膠填料的關鍵特性
為什麼選用「球形」?
1.高填充率
球形顆粒排列緊密,體積利用率高(最大達74%理論填充限)
2.高好流動性利於加工與混合,提升膠體一致性
3.降低粘度上升相較於片狀或針狀氧化鋁,球形粒子在高填充下仍保有較低混合黏度
4.分散性好減少團聚現象,維持穩定的熱傳遞路徑
三、 常見規格與挑選因素
項目 說明
粒徑大小 常見有10μm、20μm、30μm、50μm 等,粒徑大小影響流動性與導熱性。
表面處理 可做疏水處理、矽烷處理以提高相容性。
純度 一般為≥99%,純度越高,導熱性能越穩定。
比表面積 越低越好,可減少吸濕與黏度上升。
四、設計導熱膠填料的考量要素
要素 說明
粒徑分佈(PSD) 採用多峰分佈(multi-modal distribution)可提高填充率與導熱通道形成
純度 高純度可提升電氣絕緣性,降低介電損耗
熱導率 α-Al₂O₃ > 30 W/m·K,本身傳熱性能佳
介電性能 優異絕緣性(介電常數低,<10)適用於電子封裝
界面相容性 粒子表面改質(如矽烷處理)可提升與有機樹脂(如環氧、矽膠)的界面黏著性與熱傳效率
五、導熱機制
1. 傳導模式
a.固體-固體熱傳導
粒子間直接接觸傳熱為主要機制
b. 粒子連通性(percolation network)需達一定填充體積以形成熱通道
2. 影響因子因子 果
填充率(wt%) 關鍵控制參數,通常需超過70 wt% 才有明顯導熱效果
界面熱阻
(Thermal Boundary Resistance, TBR) 粒子與樹脂界面熱阻會限制熱傳效率,可藉表面修飾降低
顆粒尺寸與分佈 較大的顆粒有較低表面積,界面熱阻較小;但需與小粒子搭配以填補空隙形成連通網絡
六、填料與樹脂的相容性與處理
表面改質技術
1.矽烷偶聯劑處理(Silane Treatment)
提升與有機基材(如環氧、矽膠)之相容性與界面熱傳效率
2.氨基/環氧/羥基等官能團導入增加鍵結力
七、應用產品說明
1.導熱膠(TIM)
增強導熱膠的導熱效率並降低熱阻,常見於CPU、GPU散熱。
2.導熱矽膠片
用於LED、電源模組與電池模組,提供穩定散熱效果。
3.灌封材料
用於馬達、變壓器、電動車電池包內部,提供隔熱與保護。
4.高性能塑膠
注入工程塑膠中(如PA、PBT)製成導熱塑膠元件。
5.5G裝置材料
包含基站散熱、射頻模組,對熱管理需求高。
八、應用實例
應用產品 導熱膠型態 需求
導熱墊片(Thermal Pad) 高填充型有機聚合物+球形氧化鋁 厚度控制、熱導率 1~5 W/m·K
導熱黏著劑 環氧基膠體 高導熱與絕緣並存,要求黏結力
導熱灌封膠 雙液型矽膠系 較低黏度要求、優異流動性與絕緣性
九、與其他導熱填料的比較
填料 熱導率 價格 電氣性 填充難度
球形氧化鋁 ★★★ 中 絕緣 ★
氮化硼(BN) ★★★★ 高 絕緣 ★★
氮化鋁(AlN) ★★★★★ 非常高 絕緣 ★★★
氧化鋅(ZnO) ★★ 等偏低 半導體 ★
銀粉 ★★★★★ 非常高 導電 ★★★★
十、前沿技術與研究趨勢
1.奈米與微米混合填料設計
結合微米級(傳熱主通道)與奈米級(填補間隙)提升總體熱導率
2.球形氧化鋁複合材料
如:氧化鋁@BN 套層設計,兼具導熱與絕緣功能
3.低熱膨脹係數設計
防止熱疲勞或界面剝離,提升可靠度
4.低介電導熱材料
尤其針對 5G/AI 晶片,強調低損耗、熱控制同步
十一、實驗參考資料與性能範例(實驗設計建議)實驗項目 範圍建議
填料含量 60–90 wt%(根據樹脂黏度與應用需求)
粒徑分佈 D50 = 5~20 µm;搭配 <1 µm 奈米級填料
熱導率(複合材料) 可達 1–5 W/m·K,甚至更高
表面處理劑濃度 0.5–3 wt%(視粒子性質與樹脂而定)
十二、延伸應用研究建議
1.模擬設計
利用有限元素分析(FEA)模擬填料排列與熱場分布
2.複合填料研究球形氧化鋁 + BN、AlN 的混合體系
3.應用可靠性測試高溫老化、熱循環測試、界面剝離分析
連繫我們
Rex yang
E-mail: techrexyang@
© 2024
條款及條件